Análise de Processo de Linha de Produção
Die retrorei im technischen prozess
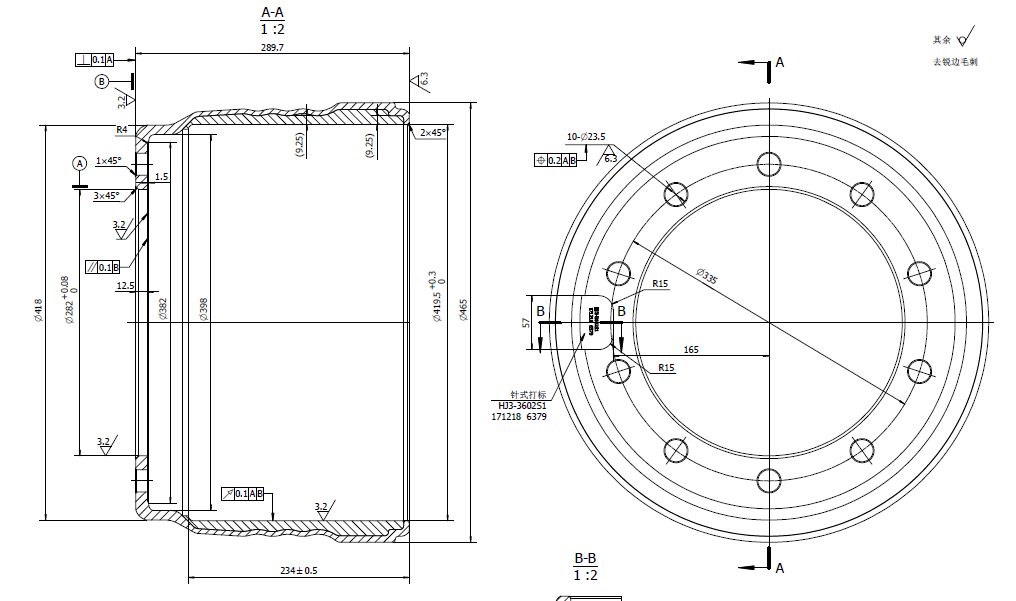
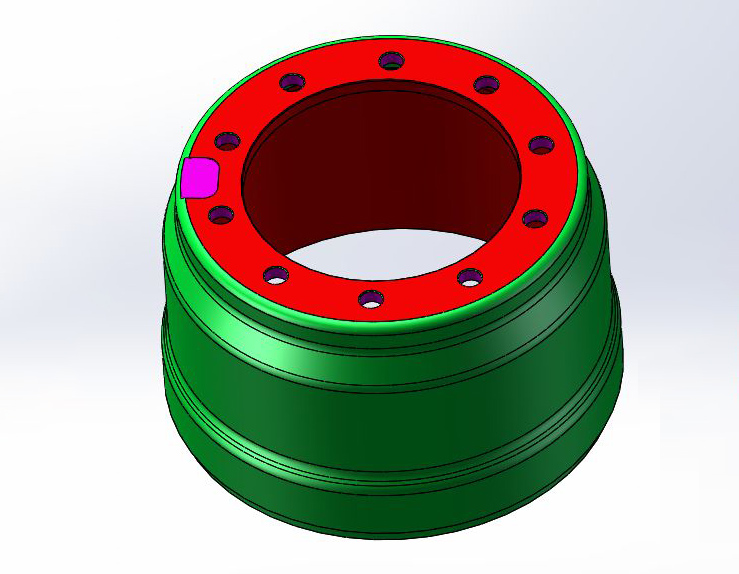
1. O processo de fixação descartável é adotado durante o torneamento. Torneamento de todas as peças usinadas, incluindo a superfície inferior das peças.
2. Durante a perfuração, devem ser utilizados grampos hidráulicos para localizar com o diâmetro interno de Φ282 e a face da extremidade superior, perfurar furos de montagem de 10-Φ23,5 e chanfrar em ambos os lados e fresar a área de marcação pneumática;
Lista de equipamentos
Temporizador de ciclo de usinagem OP10 | |||||||||||||||
Descrição da rota | ![]() | ||||||||||||||
Cliente | Material da peça de trabalho | 45 | Modelo de máquina-ferramenta | Arquivo No. | |||||||||||
Nome do produto | Peças soldadas de eixo de ferramenta de corte | Desenho nº. | Data de preparação | 19/01/2021 | Preparado pela | ||||||||||
Etapa do processo | Faca No. | conteúdo de usinagem | Nome da ferramenta | Diâmetro de corte | Velocidade de corte | Velocidade de rotação | Avanço por revolução | alimentação por máquina-ferramenta | Número de estacas | Cada processo | Tempo de usinagem | Tempo ocioso | Apertar e afrouxar | Tempo de troca de ferramentas | |
Não. | Não. | Desoripções | Ferramentas | D mm | VcM/min | Rpm | mm/Rot | mm/minuto | Tempos | Comprimento mm | Seg | Seg | Seg | ||
1 | T01 | Tornear a face superior grosseiramente | 455,00 | 450 | 315 | 0,35 | 110 | 1 | 20.0 | 10,89 | 3 | 3 | |||
2 | T02 | Tornear aproximadamente furo interno DIA 419,5, face escalonada DIA 382 e furo interno DIA 282 | 419,00 | 450 | 342 | 0,35 | 120 | 1 | 300,0 | 150,36 | 3 | 3 | |||
3 | T03 | Tornear a face final com precisão | 455,00 | 450 | 315 | 0,25 | 79 | 1 | 20.0 | 15.24 | 3 | ||||
4 | T04 | Tornear com precisão o furo interno DIA 419.5, a face escalonada DIA 382 e o furo interno DIA 282 | 369,00 | 450 | 388 | 0,25 | 97 | 1 | 300. 0 | 185,39 | |||||
5 | T05 | Tornear a face inferior de forma reversa e grosseira | 390,00 | 420 | 343 | 0,35 | 120 | 1 | 65,0 | 32,49 | 3 | ||||
6 | T06 | Tornear de forma reversa e precisa a face inferior | 390,00 | 450 | 367 | 0,25 | 92 | 1 | 65,0 | 42,45 | 3 | ||||
Descrição: | Tempo de corte: | 437 | Segundo | Tempo para fixação com dispositivo e para carregamento e corte de materiais: | 15h00 | Segundo | |||||||||
Tempo auxiliar: | 21 | Segundo | Total de horas-homem de usinagem: | 472,81 | Segundo |
Temporizador de ciclo de usinagem OP20 | |||||||||||||||
Descrição da rota | ![]() | ||||||||||||||
Cliente | Material da peça de trabalho | HT250 | Modelo de máquina-ferramenta | Arquivo No. | |||||||||||
Nome do produto | Tambor de freio | Desenho nº. | Data de preparação | 19/01/2021 | Preparado pela | ||||||||||
Etapa do processo | Faca No. | conteúdo de usinagem | Nome da ferramenta | Diâmetro de corte | Velocidade de corte | Velocidade de rotação | Avanço por revolução | alimentação por máquina-ferramenta | Número de estacas | Cada processo | Tempo de usinagem | Tempo ocioso | Apertar e afrouxar | Tempo de troca de ferramentas | |
Não. | Não. | Desoripções | Ferramentas | D mm | VcM/min | Rpm | mm/Rot | mm/minuto | Tempos | Comprimento mm | Seg | Seg | Seg | ||
1 | T01 | Furo de montagem de 10-DIA 23,5 | Broca de fundo de poço DIA 23,5 | 23,50 | 150 | 2033 | 0,15 | 305 | 10 | 15.0 | 29,52 | 20 | 5 | ||
2 | T04 | Chanfradura de orifício de 10 DIA 23 | Fresa de chanfradura e alargamento composto DIA 30 | 30,00 | 150 | 1592 | 0,20 | 318 | 10 | 3.0 | 6,65 | 20 | 5 | ||
3 | T06 | Chanfradura de orifício traseiro de 10 DIA 23,5 | Fresa de chanfradura reversa DIA 22 | 22h00 | 150 | 2171 | 0,20 | 434 | 10 | 3.0 | 4.14 | 40 | 5 | ||
4 | T08 | Área de marcação de fresagem | Fresamento de esquadro DIA 30 | 30,00 | 80 | 849 | 0,15 | 127 | 1 | 90,0 | 42,39 | 4 | 5 | ||
Descrição: | Tempo de corte: | 82 | Segundo | Tempo para fixação com dispositivo e para carregamento e corte de materiais: | 30 | Segundo | |||||||||
Tempo auxiliar: | 104 | Segundo | Total de horas-homem de usinagem: | 233,00 | Segundo |
Introdução à Linha de Produção
Layout da linha de produção
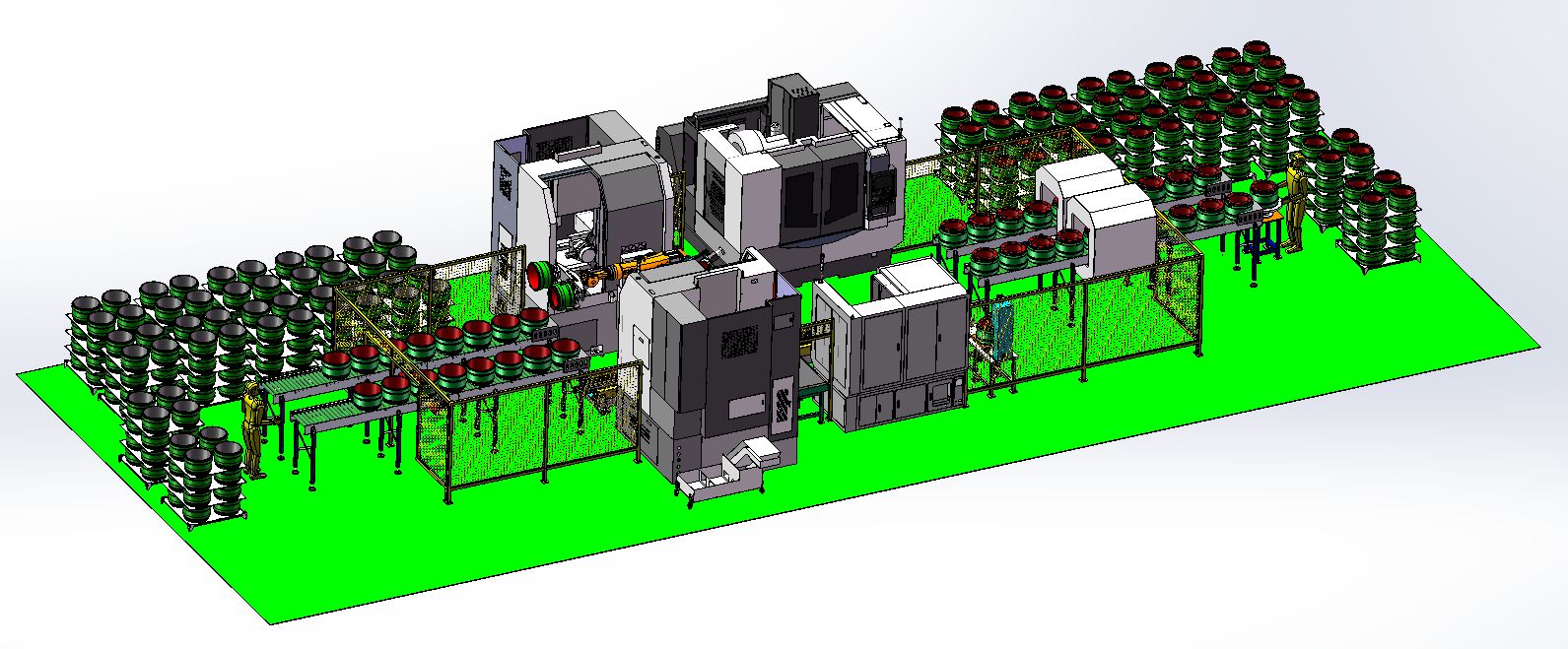
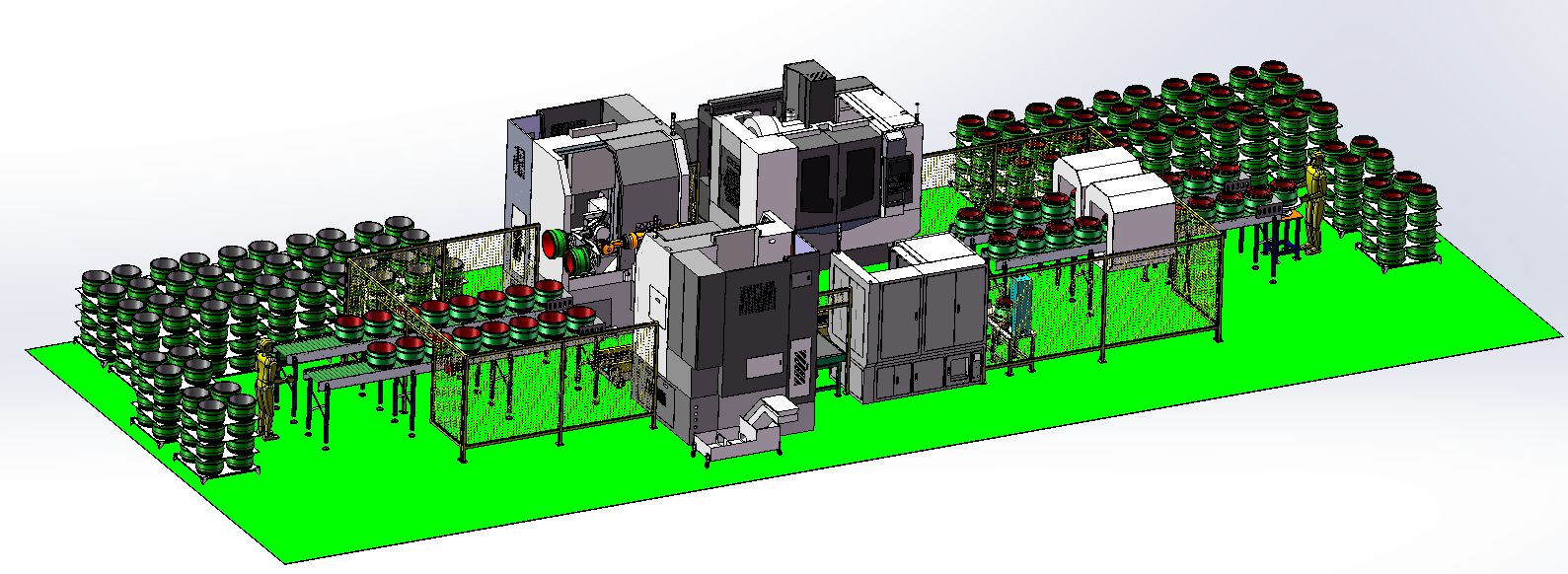
Introdução à Linha de Produção
A linha de produção é composta por 1 unidade de carga, 1 unidade de usinagem de torno e 1 unidade de corte. Robôs transportam materiais entre as estações dentro de cada unidade. Empilhadeiras posicionam cestos em frente às unidades de carga e corte. A linha de produção cobre uma área de: 22,5 m × 9 m
Descrição da linha de produção
1. As peças brutas são transportadas para as estações de carga por empilhadeiras, içadas manualmente até a plataforma de rolos e enviadas para as estações de carga através dos rolos. O carregamento e o descarregamento da máquina de balanceamento no processo de torno, o processo de laminação e o processo de furação e fresamento são realizados por robôs. Os produtos acabados são enviados para as estações de corte através da plataforma de rolos e enviados para fora pelas empilhadeiras após içamento e empilhamento manuais.
2. Telas eletrônicas de exibição em grande escala devem ser instaladas nas linhas de transmissão logística para atualizar e exibir as informações de produção, produtos defeituosos e dias de produção de segurança em tempo real;
3. A linha de transmissão deverá ser dotada de luz de advertência em cada unidade, que possa exibir informações como: normal, falta de material e alarme;
4. A linha automática adota o modo de unidade de processamento e o modo de fiação multiunidade, com layout flexível, adequado para diferentes requisitos de layout dos clientes;
5. Adote um robô conjunto para carregamento e corte, que tem alta estabilidade, manutenção conveniente e longa vida útil;
6. Baixa demanda de pessoal. A demanda diária de pessoal para cada turno desta linha automática é a seguinte:
Empilhador 1 a 2 pessoas (responsável por levantar, empilhar e transferir peças em bruto/produtos acabados)
Engenheiro de Manutenção 1 pessoa (responsável pela manutenção de rotina - cortadores de óleo e água, etc.)
7. A linha automática possui forte extensibilidade, como usinagem de fios mistos, rastreabilidade de peças e outras funções, com baixo custo de expansão;
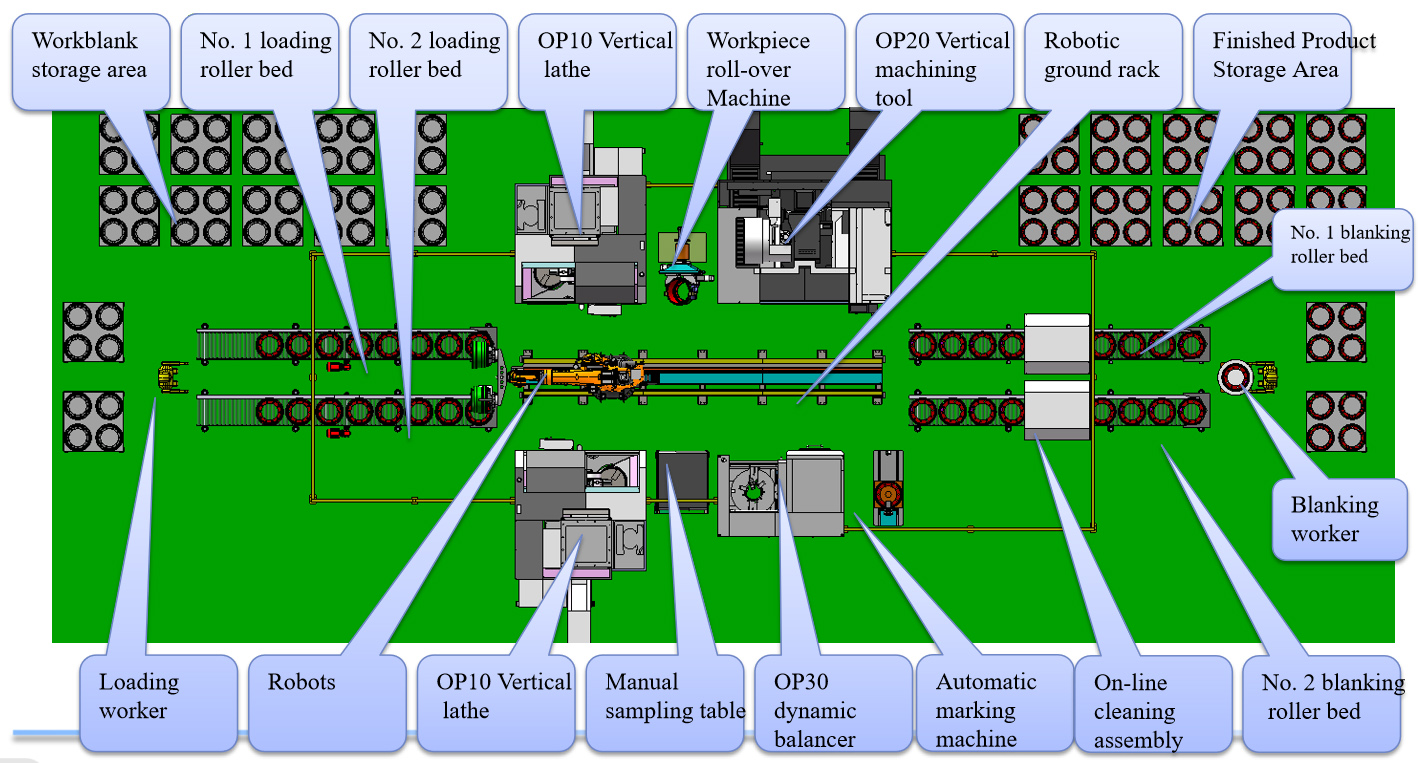
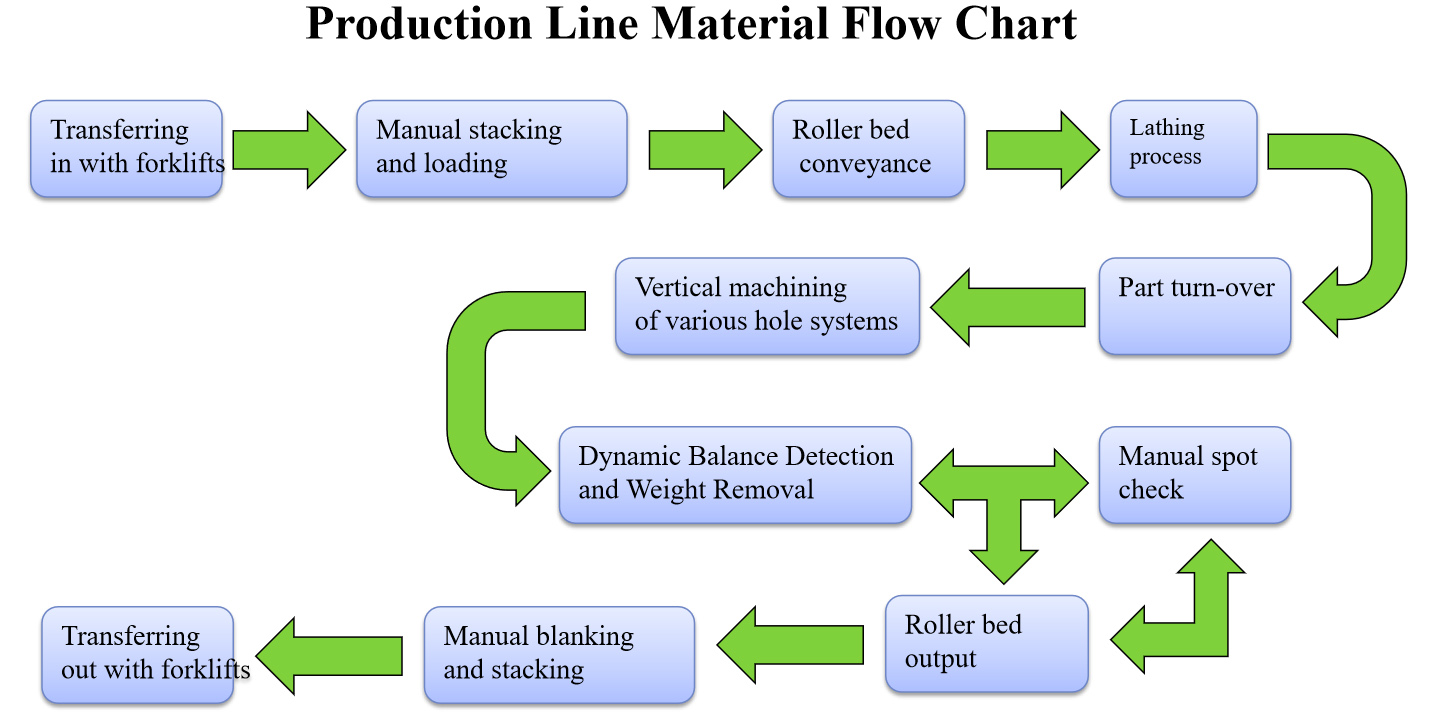
Unidade de carga
1. A linha de leito de rolos de carga pode armazenar 12×16=192 peças; 2. Abra manualmente a pilha e içe-a para o leito de rolos de carga e envie-a para a estação de carregamento pelo transportador de rolos; 3. Após a abertura da pilha, a bandeja vazia deve ser fixada e colocada na linha de corte de bandejas vazias, empilhando-as em 8 camadas, e o empilhamento da bandeja vazia deve ser removido manualmente e colocado na área de armazenamento; 1. A linha de leito de rolos de carga pode armazenar 12×16=192 peças;
2. Abra manualmente a pilha e içe-a até a plataforma de rolos de carga e envie-a para a estação de carga pelo transportador de rolos;
3. Após a abertura da pilha, a bandeja vazia deve ser fixada e colocada na linha de obturação de bandejas vazias, empilhando-as em 8 camadas, e o empilhamento da bandeja vazia deve ser removido manualmente e colocado na área de armazenamento;
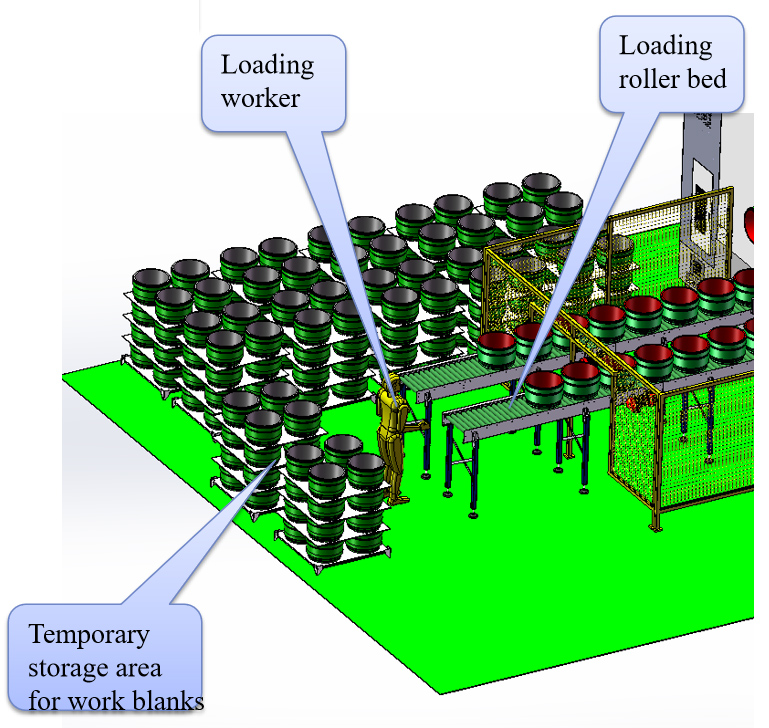
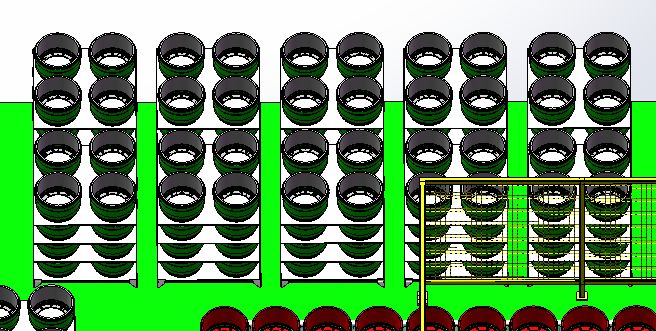
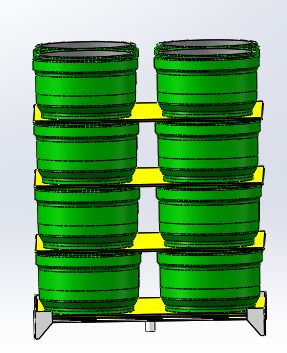
Introdução às pilhas de trabalho em branco
1. Uma pilha de 16 peças e 4 camadas no total, com placas divisórias entre cada camada;
2. A pilha de peças em branco pode armazenar 160 peças;
3. Sugere-se que o palete seja preparado pelo cliente. Requisito: (1) Boa rigidez e planura (2) Possibilidade de fixação pelo robô.
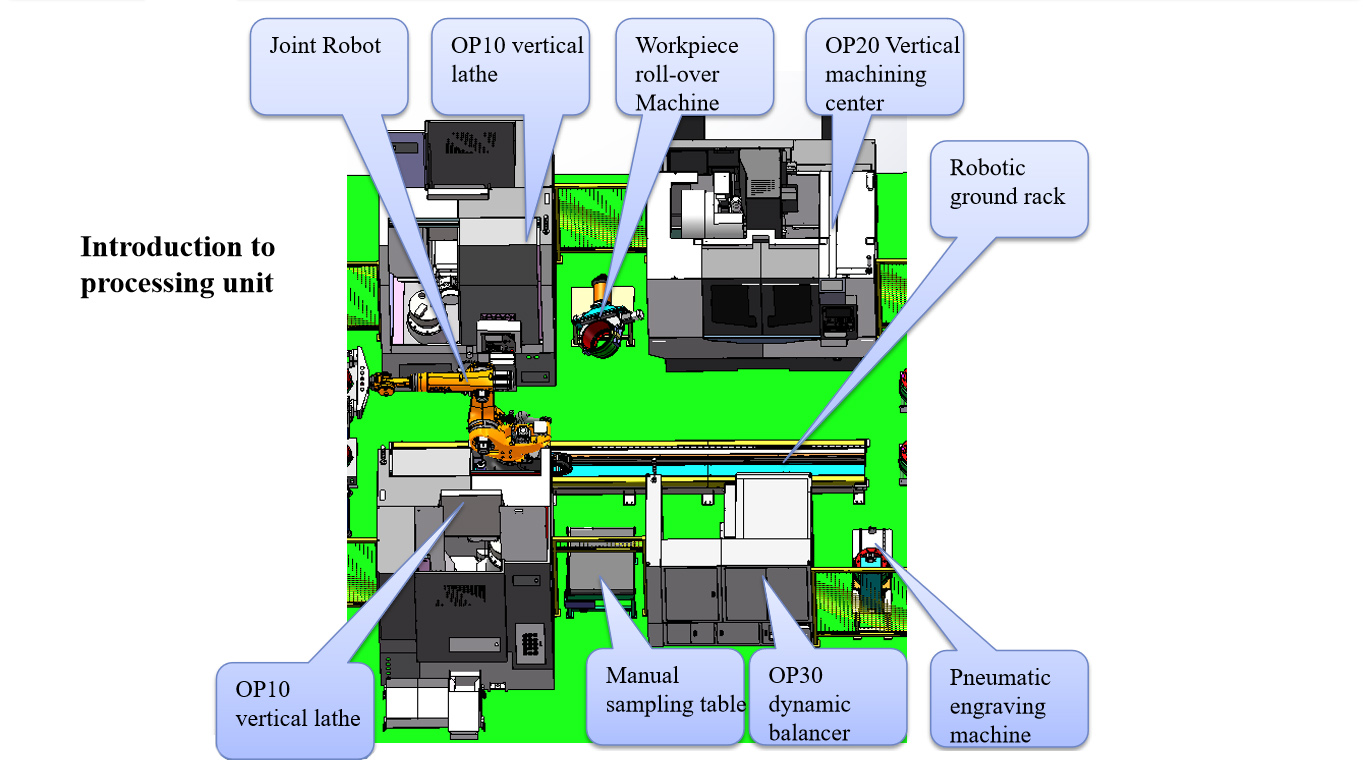
Introdução à unidade de processamento
1. O processo de torneamento consiste em dois tornos verticais, o robô nº 1 e o suporte de aterramento do robô, que realizam a usinagem do círculo externo, da superfície do degrau do furo interno e da face final da peça;
2. A estação de laminação consiste em 1 máquina de laminação, que realiza a laminação automática de peças;
3. O processo de perfuração e fresamento consiste em 1 centro de usinagem vertical e um robô nº 2, que realiza a usinagem do furo de instalação e a área de marcação desta peça.
4. O processo de balanceamento dinâmico e remoção de peso consiste em um balanceador dinâmico vertical, que realiza a detecção do balanceamento dinâmico e a remoção do peso das peças;
5. A estação de verificação manual pontual consiste em uma correia transportadora, que realiza o transporte das peças verificadas pontualmente e é usada como plataforma de inspeção;
6. A estação de trabalho da máquina de gravação pneumática realiza o trabalho de gravação e marcação de todos os produtos;
Introdução da unidade de obturação
1. A linha de cama do rolo de carga pode armazenar 12×16=192 peças;
2. As bandejas e placas divisórias na estação de carga são transportadas para a área de corte pelas empilhadeiras;
3. Os produtos acabados são transportados para a estação de corte pelo transportador de rolos, sendo içados e empilhados manualmente e transferidos com empilhadeiras;
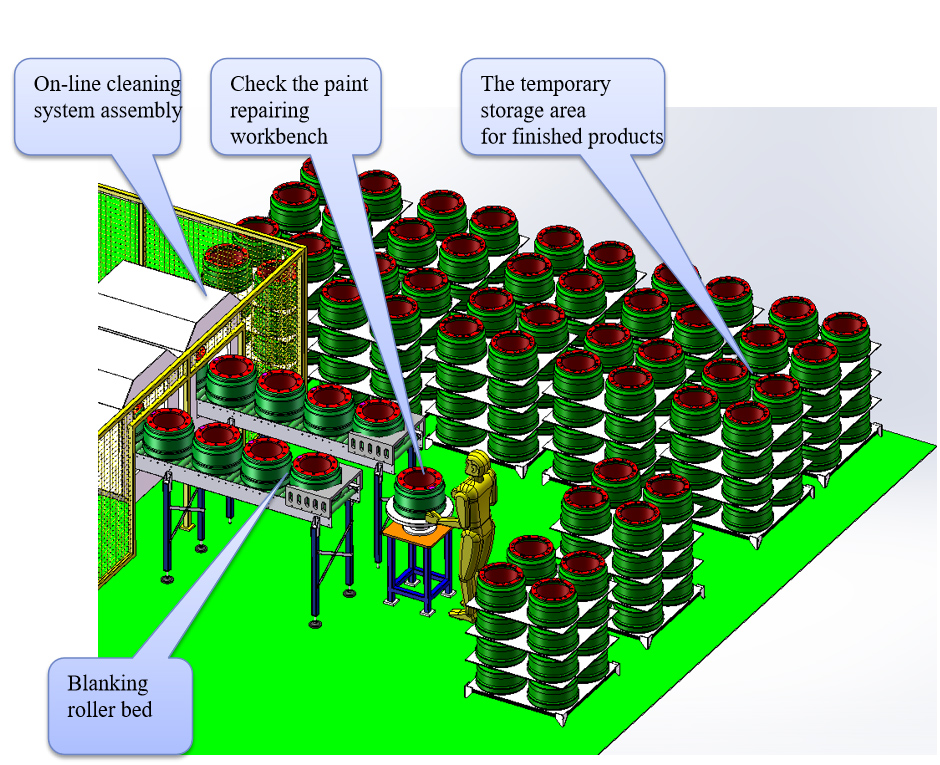
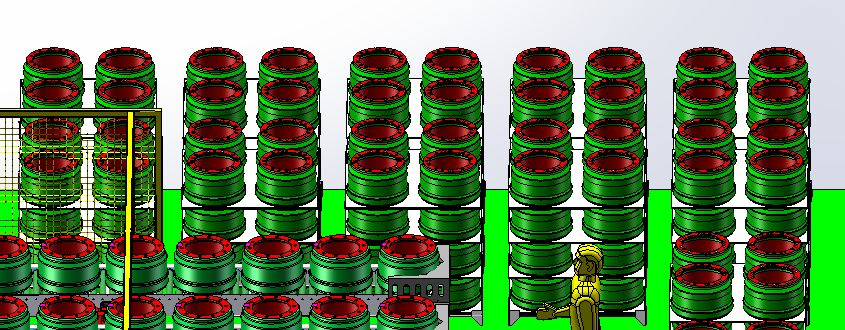
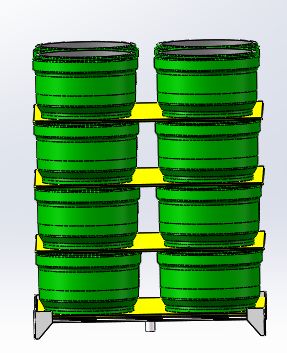
Introdução ao empilhamento de produtos acabados
1. Uma pilha de 16 peças e 4 camadas no total, com placas divisórias entre cada camada;
2.192 peças podem ser armazenadas na pilha de produtos acabados;
3. Sugere-se que o palete seja preparado pelo cliente. Requisito: (1) Boa rigidez e planura (2) Possibilidade de fixação pelo robô.
Introdução dos principais componentes funcionais da linha de produção
Introdução à Usinagem e Balanceamento Dinâmico Unidade de Remoção de Peso Robótica
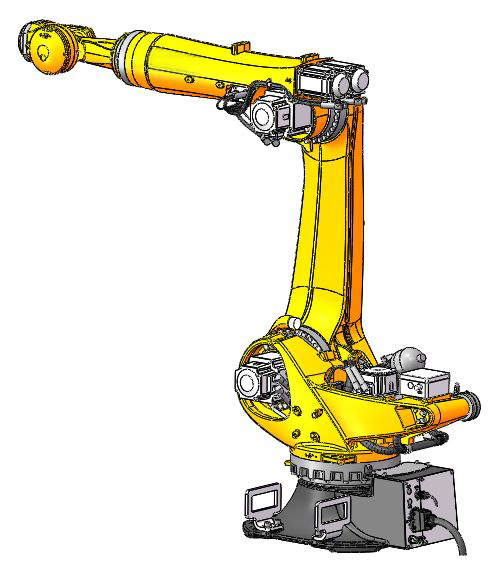
Robô Chenxuan: SDCX-RB08A3-1700
Dados básicos | |
Tipo | SDCX-RB08A3-1700 |
Número de eixos | 6 |
Cobertura máxima | 3100 mm |
Repetibilidade de pose (ISO 9283) | ±0,05 mm |
Peso | 1134 kg |
Classificação de proteção do robô | Classificação de proteção IP65 / IP67pulso alinhado(IEC 60529) |
Posição de montagem | Teto, ângulo de inclinação permitido ≤ 0º |
Acabamento de superfície, pintura | Estrutura de base: preta (RAL 9005) |
Temperatura ambiente | |
Operação | 283 K a 328 K (0 °C a +55 °C) |
Armazenamento e transporte | 233 K a 333 K (-40 °C a +60 °C) |
Introdução ao Eixo de Viagem do Robô
A estrutura é composta por um robô articulado, um servomotor e um pinhão e cremalheira, permitindo que o robô realize movimentos retilíneos para frente e para trás. Ele desempenha a função de um único robô, servindo a múltiplas máquinas-ferramentas e segurando peças em diversas estações, podendo aumentar a cobertura de trabalho dos robôs articulados.
A esteira rolante aplica a base soldada com tubos de aço e é acionada por servomotor, pinhão e cremalheira, para aumentar a cobertura de trabalho do robô articulado e melhorar efetivamente a taxa de utilização do robô;
A pista de viagem é instalada no solo;
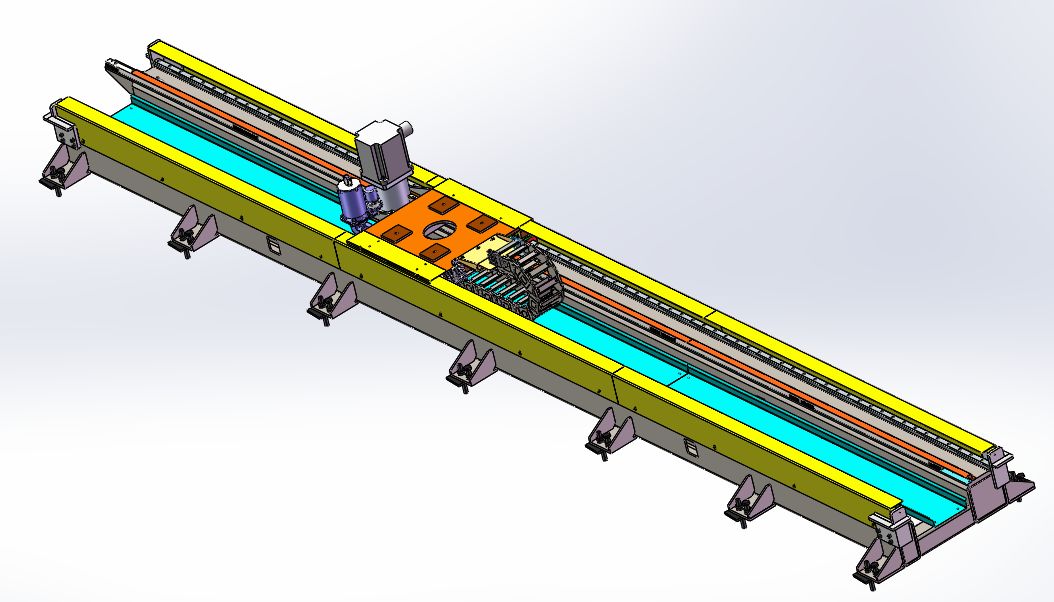
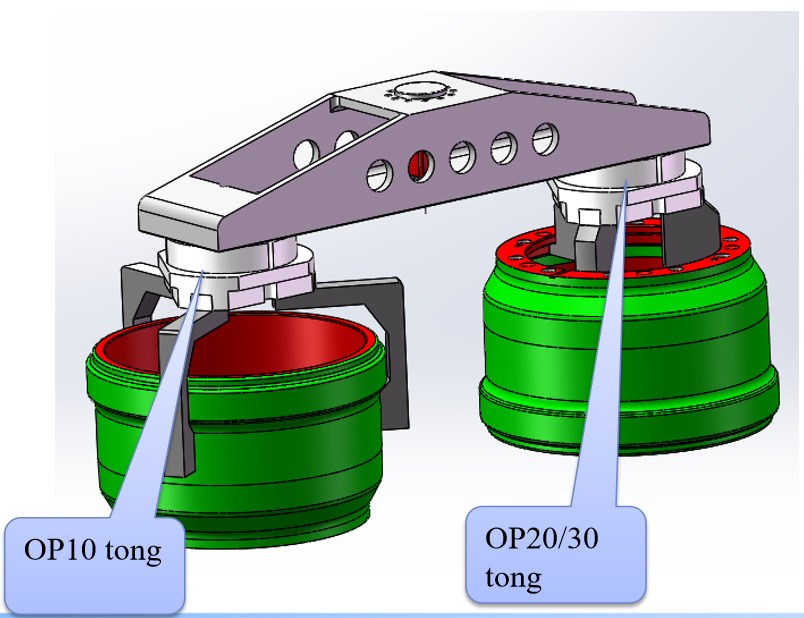
Introdução de pinças de robôs de carregamento e corte
Descrição:
1. De acordo com as características desta parte, adotamos uma superfície de onda externa de três garras;
2. O mecanismo é equipado com o sensor de detecção de posição e o sensor de pressão para detectar se o status de fixação e a pressão das peças estão normais;
3. O mecanismo é equipado com um pressurizador, e a peça de trabalho não cairá em um curto espaço de tempo em caso de falha de energia e corte de gás do circuito de ar principal;
Introdução da Máquina de Roll-over Automática
Descrição:
O mecanismo é composto por uma estrutura fixa, um conjunto de base de suporte e um conjunto de pinça pneumática. Possui função anti-soltura e anti-queda após o corte de ar, e pode realizar rotação de 180° sobre as peças de trabalho da linha;
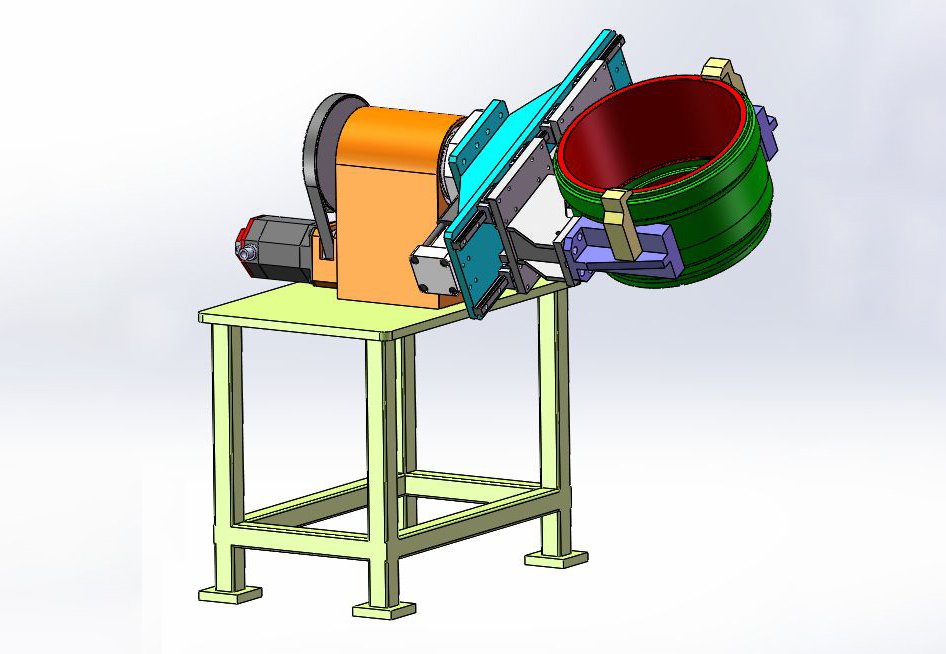
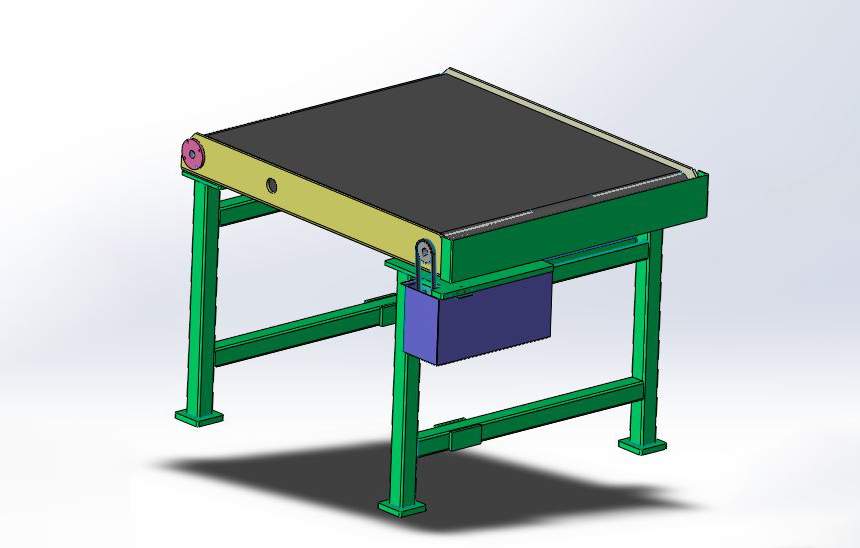
Introdução à bancada de verificação manual de pontos
Descrição:
1. Defina diferentes frequências de amostragem aleatória manual para diferentes estágios de produção, o que pode supervisionar efetivamente a eficácia da medição on-line;
2. Instruções de uso: O manipulador posicionará a peça de trabalho na posição definida na bancada de verificação pontual, de acordo com a frequência definida manualmente, e emitirá um sinal luminoso vermelho. O inspetor pressionará o botão para transportar a peça de trabalho para a área de segurança fora da área de proteção, retirará a peça de trabalho para medição e a retornará à mesa de rolos após a medição;
Componentes de proteção
É composto de perfil de alumínio leve (40×40) + malha (50×50), e a tela sensível ao toque e o botão de parada de emergência podem ser integrados aos componentes de proteção, integrando segurança e estética.
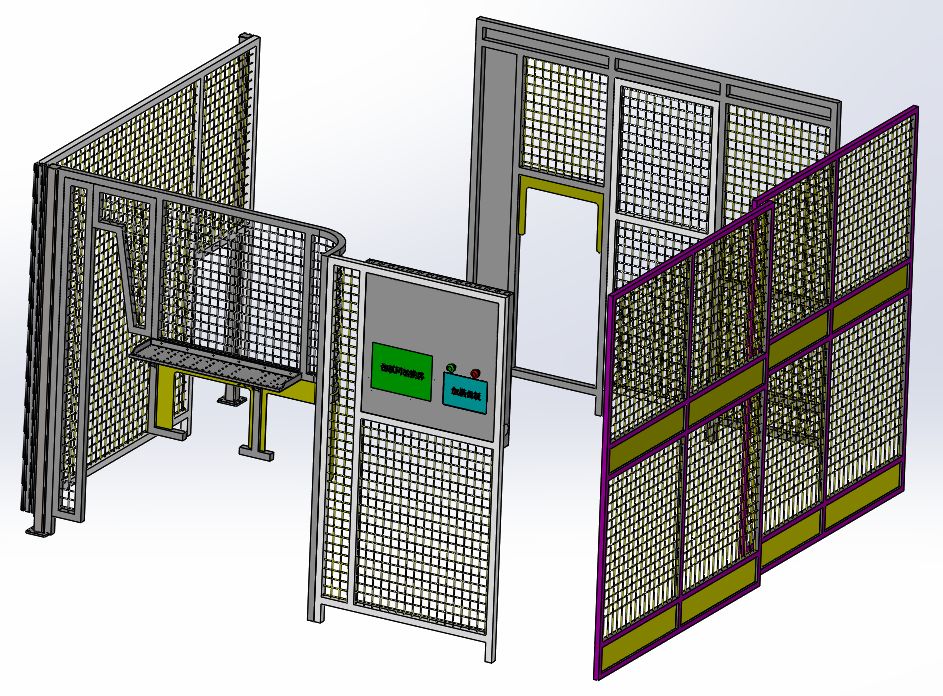
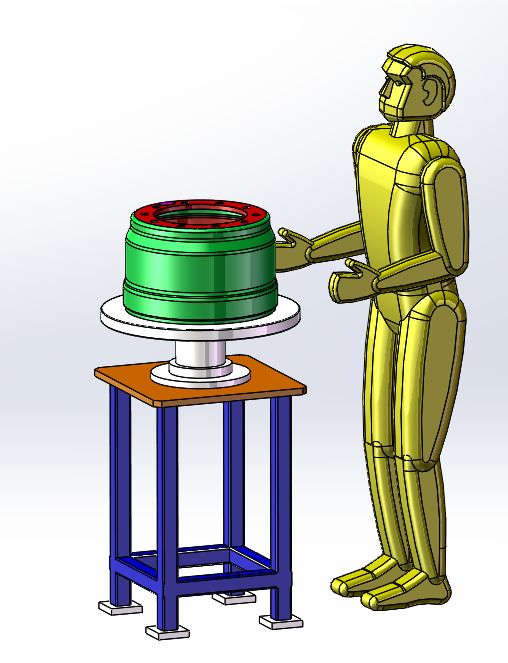
Introdução à Estação de Inspeção para reparo de pintura
Descrição:
O mecanismo é composto por uma estrutura fixa e uma plataforma giratória. A equipe levanta os produtos acabados até a plataforma giratória, gira a plataforma giratória, verifica se há batidas, arranhões e outros fenômenos, e repara oportunamente os defeitos causados por batidas e a superfície da pintura;